A Collaborative Work Environment (CWE) for asset-intensive companies in the world.
2 service stages, adjusted to your challenges
Stage A
3D & 4D
If you require a detailed modelling of the plant, a Virtual Tour, Telepresence and Remote Assistance by Experts.
Stage B
5D, 6D & 7D
Data Layer, used mostly for Efficiency Improvements, secure integration with suppliers, IoT, Asset Management with Serial Numbers, Predictive Maintenance Programs.
Stage A
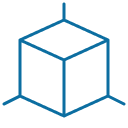
3D level
Computer-Aided Design (CAD) data.
A 3 D Model of the industrial facility that may come from the original design or may be created by modelling an existing facility after scanning it using a 3 D Laser Scanner, and modelling the resulting point cloud into a 3 D CAD format.
Service:
Talent Swarm provides the necessary qualified personnel and equipment required to perform 3 D scans of existing facilities and the detailed “As-Built” modelling in the CAD program desired by the Client. We work with Autodesk Revit, Intergraph SP3D, AVEVA E3D and others.

4D level
Adds the element of time to the 3D Model.
This involves the method to easily update the Digital Twin as changes are made to its corresponding industrial asset.
SERVICE:
Using WiFi with geolocation services, Talent Swarm may provide a real-time videogame-like visualization of the movement of equipment and personnel within the plant.
The same WiFi installation, combined with Telepresence solutions such as Eyebee® Remote Expert, Realwear HMT-1, and Hololens® from Microsoft, Talent Swarm provides contextual collaborative remote assistance environments to solve complex problems.


Stage B
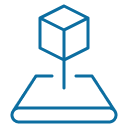
5D level
Generic identity to objects
5D adds generic identity to objects to enable connectivity to corporate ERP systems, including purchasing, logistics and secured by Blockchain audit trail to enhance security.

6D level
Create Smart Objects

6D adds profound detailed discrete information regarding each object, to create “Smart Objects” (including IoT streams and worker geolocation) for enhanced safety and faster maintenance and better service throughout the entire lifecycle of the industrial plant (PLM).

7D level
Mathematical modeling
7D incorporates mathematical modeling of the industrial process and integration with the control system programming to create “sentient”, self-diagnosing systems that add analysis of historical operation to enhance efficiency and safe operation, with prescriptive maintenance to avoid unscheduled shutdowns.

Questions and answers
I hear a lot of talk about “Digital Twins”, what are they and what are its benefits?
Most of us are still alive today thanks to the flight simulators used by pilots to practice and improve their skills in routine and extreme conditions. Yet we live close to complex and potentially dangerous industrial and energy plants designed and built decades ago.
A Digital Twin is a virtual copy of an industrial plant that allows its owner/operators, just like a cockpit simulator, to monitor it in an intuitive visual manner in real time.
This leads to greater efficiency and safety in operation, integration with maintenance software to avoid unscheduled shutdowns and the collaborative immersive environment provided by Talent Swarm allows companies to pool the knowledge and experience of their global employees to solve complex issues faster and save best practices for training.
What is the bottom line, what are the quantifiable benefits?
Reduction in Total Cost of Ownership (TOC)
Increased availability
Reduction in reactive maintenance
Incident reduction
Gain in employment productivity
How is a Digital Twin created?
If the industrial or energy plant is under construction or brand new, the 3D CAD drawings may be converted to create an initial Digital Twin.
In plants that have been operating for a while, and may have been extensively modified from the original “As Built” plans, laser scans of the plant are performed that create “point clouds” of millions of precise 3D measurements, which are later converted to exact 3D CAD models.
How do I know what equipment I have in my plant?
As with all equipment inventories, one must document in detail everything in the plant.
Talent Swarm provides a precise grid plan that simplifies this procedure so that one done, it is saved forever. This step geolocates all the equipment so that Computerized Maintenance Management Systems (CMMS) integrated with Talent Swarm may direct workers precisely to the necessary repair areas.
How long does 3D Scanning take?
Scanning a complex industrial facility takes about one 8-hour day per 1000 square meters on site, with at office processing and modelling of the resulting point cloud between 3 and 7 days per day of scanning, depending on the complexity and density of equipment in the environment.
How much can it cost to create an initial Digital Twin?
The first step of scanning and modelling an industrial facility can cost between 4 and 15 euros per square meter, plus travel and lodging costs for a team of 3 people during the scanning process.
After scanning, what are the next steps?
After scanning and 3D CAD modelling of the plant, the next steps may include:
- Inventory and geolocation of all the equipment in the plant using grid maps.
- Installation of fast WiFi Mesh coverage in the plant to perform Telepresence and remote assistance operations.
- Documentation of maintenance, supplier and costs for the inventoried equipment, including serial numbers.
- Connection and integration with computerized maintenance systems and SCADA signals.
- Connection and integration with ERP, purchasing and logistics departments.
- Documentation of Process & Instrumentation (P&ID) diagrams to collect process, flow and control information.
- Integration with industrial automation programming, historical operation archives and mathematical simulation programs to anticipate complex operation of the plant.
Why choose Talent Swarm for my Digital Twin journey instead of another company?
Talent Swarm firmly believes that all data should completely belong to the customer, forever and that the data should be saved in international, non-propietary standards. This is not the case with all suppliers of Digital Twin creation.
Please contact us to see how your expertise can make better Digital Twins for our shared clients.
Cases
Collaborative intelligence
As its company name suggests, the collaborative intelligence that results from the best minds working together generates valuable and disruptive innovation for quantum improvements in industrial plant management.