The collaborative intelligence that results from the best minds working together generates valuable and disruptive innovation for quantum improvements in industrial plant management.
The network
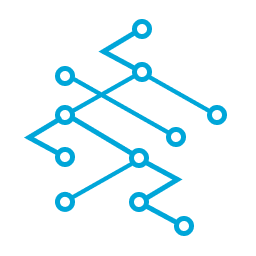
Talent Swarm has brought together some of the best expert technology companies and R&D institutions from Europe
Talent Swarm has created a a highly qualified and skilled group very knowledgeable in the latest digital technologies
motivated to create the Collaborative Working Environment using Big Data, BIM, Point Cloud scans, 3D Rendering, Videogame technology, AV/VR, Industrial IoT and complex mathematical modelling of industrial processes.
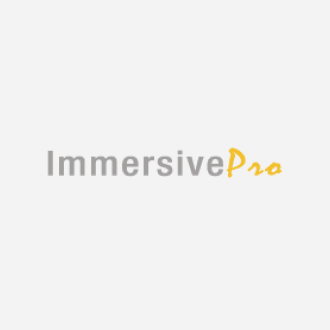
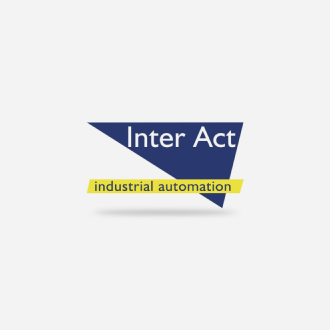
Operating processes and production sites remotely
Benchmarking of remote processes
Generating management reports of remote production locations
Remote process engineering via the cloud
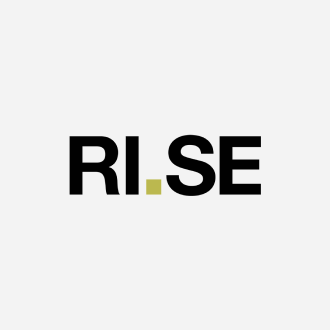

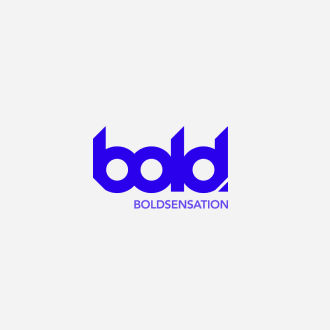

Since 2008 we work around the world for small, medium and large companies, start-ups, agencies and government entities.
We provide a creative, technological and humanistic vision to transform communication strategies and needs into visual tools for dialogue with users.

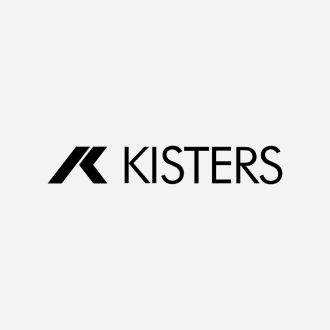
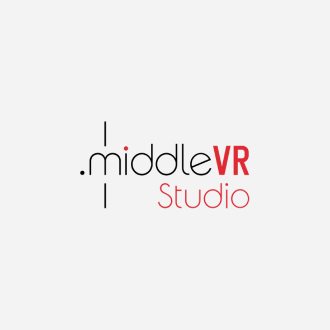
Prototyping: experience a car or a plane before it exists to improve its design and ergonomy.
Training: a wide range of training can be improved through VR, from surgeons’ gestures to maintenance or safety training.
Therapy: VR is an incredible tool for therapists to cure patients through exposure therapy.
Architecture: live and feel your project from inside as if it already exists. We want to help you focus on your applications to create better and more immersive experiences by providing you with powerful and easy-to-use tools.
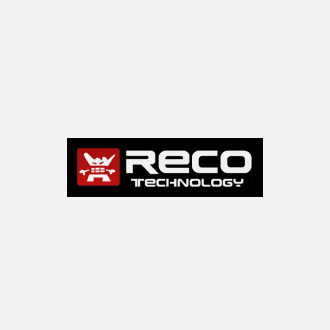

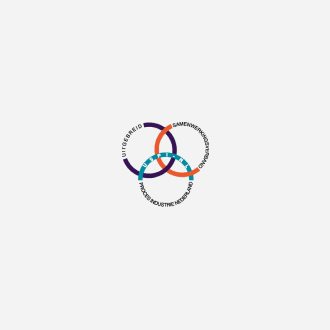
Owner Operators - an industry recognized standard would reduce the effort required to specify and communicate the information requirements to the supply chain leading to lower costs. It will also become more advantageous to move from company standards with high cost of maintenance to international ISO standards. Also the cost of mapping the handover information to the current systems of operation, engineering and maintenance will be reduced.
Contractors - a consistent approach to information handover requirements from Owner Operators would allow Contractors to integrate the information requirements into their corporate business processes and systems resulting in more efficient delivery and improved quality of the information. Currently Contractors are issued different requirements for each project or are expected to propose what should be delivered and how.
Equipment Suppliers - similarly to Contractors, a standard definition of information requirements would provide suppliers with a consistent view of requirements enabling the information to be generated once and reused.
Software Vendors - a clear definition of the core information requirements would provide clarity in the functionality needed by the industry in the tools that the develop.

Do you want to be one of our collaborators?
Benefits of being a Talent Swarm Partner and Collaborator
Industry 4.0 and BIM are inherently about shared standards and collaboration. It is unlikely and not advisable that only one company supply all the elements of the new technology that will make the 4th Industrial Revolution possible. This is why Talent Swarm’s business model is based upon bringing together the “best of breed” in the various areas that are needed to create a truly world-class solution. Customers need guidance to avoid the pitfalls of improper application of advanced technology, and the collective knowledge and experience of the Talent Swarm partners help reap the best rewards for their proactive approach to digitalization.
Collaboration takes more courage than competition, but the rewards are much greater…!
Please contact us to see how your expertise can make better Digital Twins for our shared clients.
Questions and answers
I hear a lot of talk about “Digital Twins”, what are they and what are its benefits?
Most of us are still alive today thanks to the flight simulators used by pilots to practice and improve their skills in routine and extreme conditions. Yet we live close to complex and potentially dangerous industrial and energy plants designed and built decades ago. A Digital Twin is a virtual copy of an industrial plant that allows its owner/operators, just like a cockpit simulator, to monitor it in an intuitive visual manner in real time. This leads to greater efficiency and safety in operation, integration with maintenance software to avoid unscheduled shutdowns and the collaborative immersive environment provided by Talent Swarm allows companies to pool the knowledge and experience of their global employees to solve complex issues faster and save best practices for training.
What is the bottom line, what are the quantifiable benefits?
Reduction in Total Cost of Ownership (TOC)
Increased availability
Reduction in reactive maintenance
Incident reduction
Gain in employment productivity
How is a Digital Twin created?
If the industrial or energy plant is under construction or brand new, the 3D CAD drawings may be converted to create an initial Digital Twin. In plants that have been operating for a while, and may have been extensively modified from the original “As Built” plans, laser scans of the plant are performed that create “point clouds” of millions of precise 3D measurements, which are later converted to exact 3D CAD models.
How do I know what equipment I have in my plant?
As with all equipment inventories, one must document in detail everything in the plant.
Talent Swarm provides a precise grid plan that simplifies this procedure so that one done, it is saved forever. This step geolocates all the equipment so that Computerized Maintenance Management Systems (CMMS) integrated with Talent Swarm may direct workers precisely to the necessary repair areas.
Al igual que todos los inventarios de equipos, uno deberá documentar en detalle todo lo que contiene la planta.
Talent Swarm proporciona una cuádricula precisa que simplifica este proceso para que una vez hecho, se guarda para siempre. Este paso geolocaliza todos los equipos para que los Sistemas de Gestión de Mantenimiento (CMMS en inglés) integrados con Talent Swarm puedan dirigir con precisión a los trabajadores a las zonas de reparaciones necesarias.
How long does 3D Scanning take?
Scanning a complex industrial facility takes about 1 8-hour day per 1000 square meters on site, with at office processing and modelling of the resulting point cloud between 3 and 7 days per day of scanning, depending on the complexity and density of equipment in the environment.
How much can it cost to create an initial Digital Twin?
The first step of scanning and modelling an industrial facility can cost between 4 and 15 euros per square meter, plus travel and lodging costs for a team of 3 people during the scanning process.
After scanning, what are the next steps?
After scanning and 3D CAD modelling of the plant, the next steps may include:
1. Inventory and geolocation of all the equipment in the plant using grid maps.
2. Installation of fast WiFi Mesh coverage in the plant to perform Telepresence and remote assistance operations.
3. Documentation of maintenance, supplier and costs for the inventoried equipment, including serial numbers.
4. Connection and integration with computerized maintenance systems and SCADA signals.
5. Connection and integration with ERP, purchasing and logistics departments.
6. Documentation of Process & Instrumentation (P&ID) diagrams to collect process, flow and control information.
7. Integration with industrial automation programming, historical operation archives and mathematical simulation programs to anticipate complex operation of the plant.
Why choose Talent Swarm for my Digital Twin journey instead of another company?
Talent Swarm firmly believes that all data should completely belong to the customer, forever and that the data should be saved in international, non-propietary standards. This is not the case with all suppliers of Digital Twin creation.